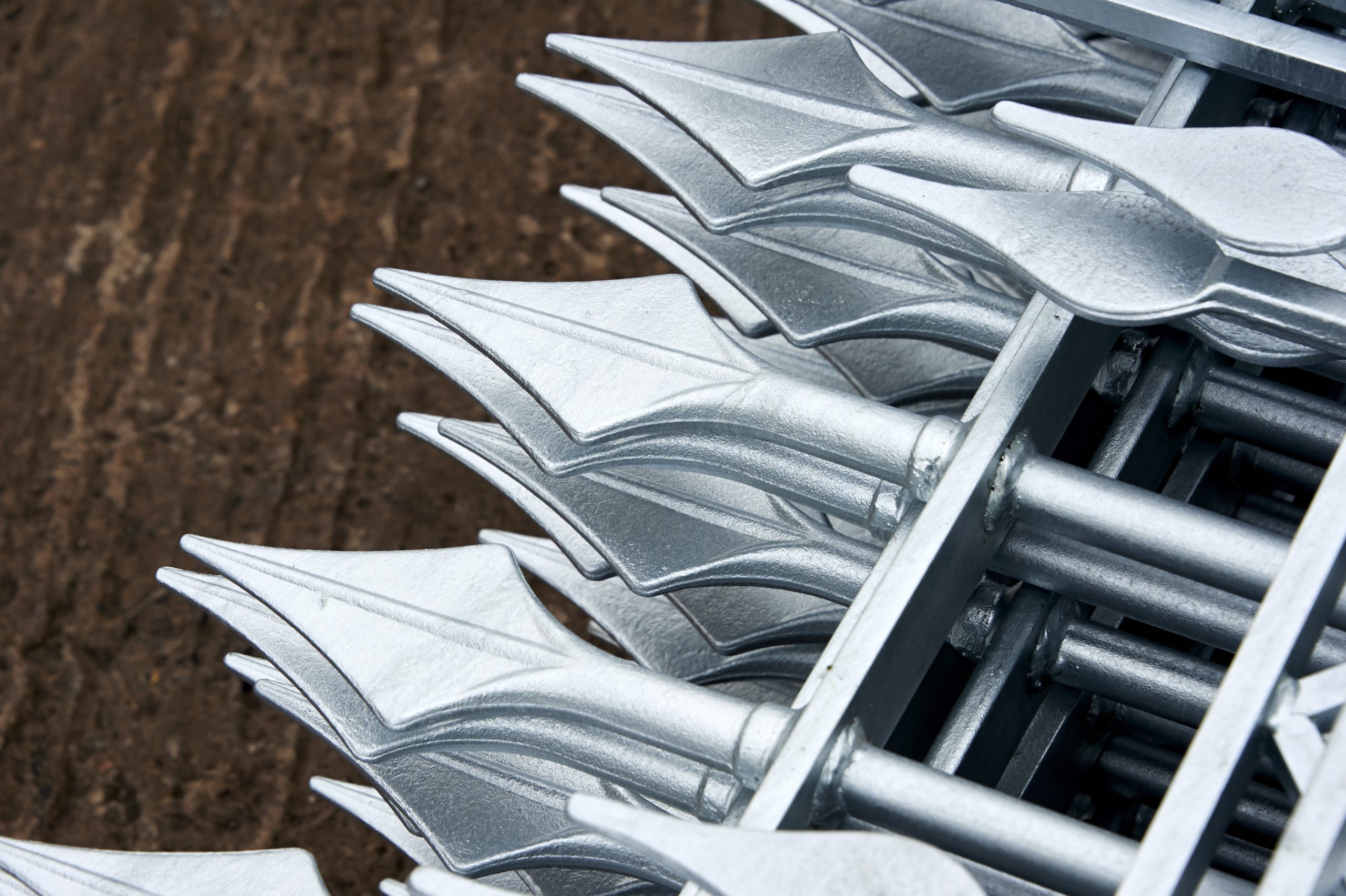
Need a hand? Just let us know
Frequently Asked Questions
Galvanized steel is one of the most durable and cost-effective solutions for corrosion protection. But how long does it actually last? The lifespan of galvanized steel depends on environmental conditions, but it is not uncommon for galvanized steel to last more than 70 years under certain conditions.
Latest corrosion rates in your area can be found at the Galvanizers Association.
Yes, galvanized steel’s zinc coating is highly resistant to abrasion. This makes galvanized steel a good choice for outdoor structures and other applications where abrasion is a concern.
The zinc coating is tough because it’s made of a series of zinc-iron alloy layers. The outer layer of zinc absorbs shock, while the harder alloy layers beneath protect against abrasion.
The zinc coating is metallurgically bonded to the steel, making it an integral part of the steel surface.
The Zinc corrodes in preference to steel and sacrifices itself to protect the steel, hence hot dip galvanizing will provide this sacrificial protection
“White Rust”, or wet storage stain, is formed because zinc on newly-galvanized steel is very reactive and quickly forms zinc oxide and zinc hydroxide corrosion products that go on to become the stable zinc carbonate.
When galvanized steel is stacked damp, stored in wet boxes or shrink wrapped with no free-flowing air, the zinc forms excessive layers of zinc hydroxide, otherwise known as wet storage stain.
Most wet storage stain can be easily removed with a nylon brush. To prevent wet storage stain, store galvanized steel indoors and in such a way to allow free-flowing air between each galvanized item.
The chemistry of the steel is the main influence on coating thickness and appearance.
Products manufactured by steel companies can include different chemical properties, leading to different coating appearances.
The galvanizer may also use several different additives in their galvanizing bath to enhance the coating appearance by making it shiny, spangled or minimising the reactivity of certain steel chemistries.
The appearance of the coating does not change the corrosion protection of the zinc coating.
Depending on the product and condition of the steel surface, the initial cost of galvanizing can be the same as a good quality paint system.
However, when the lifetime cost of a project is considered, galvanizing can provide up to 70 years maintenance-free, while paint systems will require maintenance or reapplication at various intervals – meaning costs can be considerable in the long run.
Hot-dip fasteners generally have about 10 times as much zinc on the surface and are suitable for use in all exterior and interior applications.
Zinc-plated fasteners will provide a disappointing performance if used outside, especially when used to connect hot-dip galvanized structural steel.
The main reason for these holes is to allow trapped air and gases to escape. It also enables cleaning chemicals and molten zinc to flow throughout the fabrication and then back into the tank.
Because of the temperatures involved in the galvanizing process, there is a significant risk of explosion when any trapped air is rapidly heated in the galvanizing bath.
Your local Wedge plant will be able to provide free technical advice on venting and drainage to give you the best possible finish. Alternatively for more information, visit our Venting Procedures Page.
There is no such thing as ‘cold’ galvanizing.
The term is often used in reference to painting with zinc-rich paint. Galvanizing requires heat in order to produce the metallurgical bond between coating and steel that gives galvanizing its long life and hard-wearing characteristics.
Hot dip galvanizing is essentially the process of coating clean steel with a layer of molten zinc to protect the it from corrosion and provide a long-lasting, durable surface. It’s more robust than other coatings that only bond chemically or mechanically, and it has the added advantage of fully coating the steel. As a finish, it is not only highly effective, but is also extremely eco-friendly. A single, one-off treatment will coat a product both inside and out, providing a finish which can protect steel and keep it maintenance-free for up to 60 years, or even more in the right conditions.
Any molten zinc which does not instantly form a metallurgic reaction with the steel to coat it remains in the galvanizing bath to be reused again and again. Due to zinc’s non-ferrous properties, it can be reused repeatedly without having any negative impact on its chemical constitution.
The galvanizing process uses substantial volumes of water during the steel cleaning stage, whereby all chemicals are rinsed away with cold water. More water is used during the cooling process, which involves galvanized steel being placed in a tank of cold water so that it can be handled (after reaching temperatures of 450 degrees).
To minimise water usage, Wedge Group Galvanizing have a rainfall collection system at their sites to ensure any rainfall that falls on to the roofs of plants is collected and stored on-site through a series of gutters and tanks, to be recycled back into the galvanizing system.
Galvanizing is effective in even the harshest of environments – providing maintenance-free protection against a wide range of corrosive elements such as rain and snow, marine locations, and industrial and chemical processes.
This means that the whole life costs of products protected by the hot-dip galvanizing process can be significantly reduced because there is no need for the expense, down-time and inconvenience of repeated on-site maintenance or replacement.
While the Galvanizing industry has historic roots (it dates back to the mid-1700s), the emergence of new technologies and continuing investment by the industry means that galvanizing – today as valuable to a diverse range of sectors as it’s ever been – is a process that has absolutely moved with the times.
Developments such as high-velocity ‘smart’ furnaces, fume extraction units, and heat recovery systems have helped to optimise production and enhance performance, whilst the introduction of equipment such as inverters has delivered significant savings in power consumption.
And, though the metallurgy has remained largely the same over the centuries, that’s now changing too – with the Wedge Group becoming the first galvanizing organisation in the UK to take the ambitious decision to completely remove lead and chrome from its process.
Do You Have A Question? We’re Here To Help
CALL +44 (0)1902 60194
EMAIL INFO@WGGLTD.CO.UK
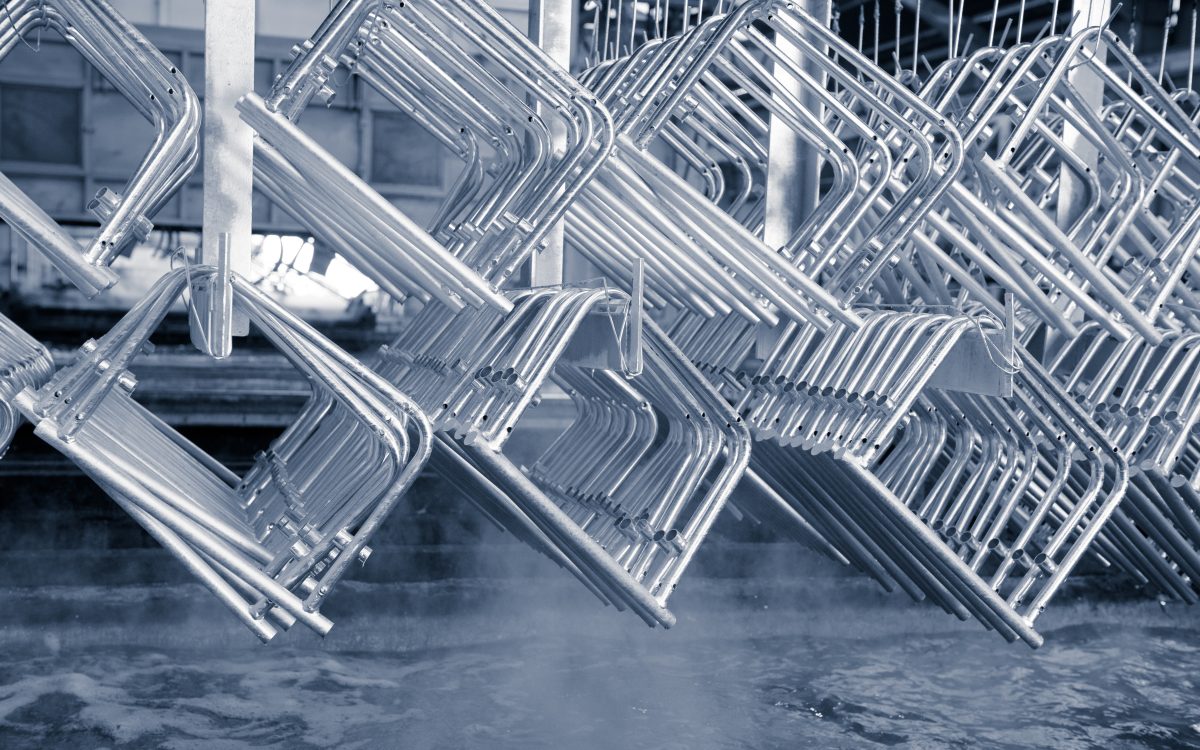